Dashboard
- Analyze asset performance metrics.
- Identify recurring failures and expedite resolution.
- View spare parts requirements and usage trends.
- Review unplanned material usage.
- Review and act on cost overrun and scheduling delays.
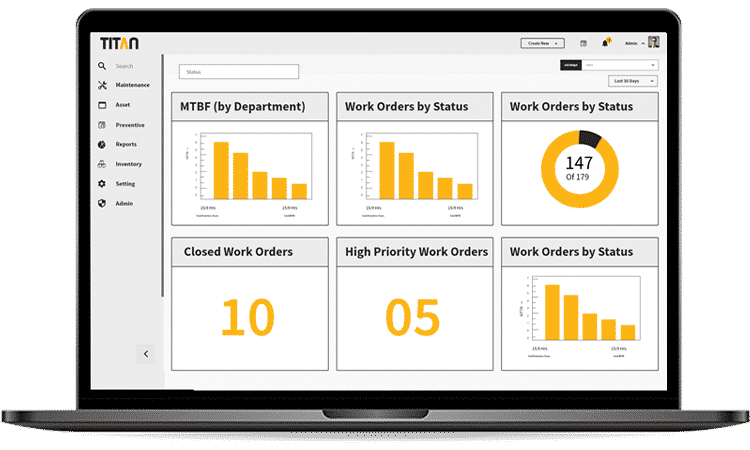
Get Your Free Demo Today!
Titan CMMS provides solution for businesses to automate all maintenance routines and helps to reduce breakdowns and increase revenue.
TITAN CMMS (Computerized Maintenance Management System Software) helps all businesses automate their maintenance management, reducing breakdowns and increasing revenue. Free CMMS Maintenance Software by TitanCMMS is also designed for planning and budgeting, deferred maintenance, capital improvements, equipment repairs, replacements and construction projects. By standardizing maintenance procedures, scheduling work tasks and tracking work orders. It also improves inventory management, offers detailed reporting for data-driven decisions, and ensures compliance with industry audits and certifications.
Advanced features: like predictive maintenance, automated alerts and customizable dashboard.
When you implement a computerized maintenance management system, you can expect to realize these benefits:
TITAN CMMS enable you to connect your plant and machinery to your maintenance management system through smart sensors and other IIOT techniques. This enables your maintenance management system to be smart enough to generate and schedule maintenance activity requirements automatically for assets
We have reduced our yearly maintenance budget 25%-30% by efficiently planning the maintenance and productively use our resources with TITAN. We have improved resource utilization up to 60% and we have reduced 40% work force allocated for maintenance. maintenance is not centric to specific person but anyone who uses TITAN can fix most problems. We have reduced downtimes of production by 50%. Maintenance couldn’t have been a simple job without TITAN.
MUDASSIR SALEEM (Managing Director of Salim Winding Works- Candle Threads)
A Computerized Maintenance Management System is the best way for an organization to manage its maintenance tasks such as planning, monitoring and reporting. This is to say that it helps them to improve the reliability of their equipment, reduce the time taken before a problem in the machine can be noticed, manage spare parts well as well as increase the life span of assets through better ways of maintaining them.
When selecting a CMMS it is important to keep in mind things such as preventive maintenance scheduling, work order management, asset management, stock control, mobile access, reporting and analytics, integration with other systems (either ERP or IoT devices) and easy operation. These features guarantee thorough maintenance management customized to your company’s requirements
Absolutely, CMMS software is versatile and can benefit different sectors including manufacturing, healthcare, facilities management, education, hospitality among others. Its versatility comes from the fact that it can handle maintenance of diverse assets and facilities thus it can pretty much suit any organization whose the function depends on equipment or facilities maintenance
Several essential steps are involved in the adoption of a CMMS: planning and goal setting, asset inventory and data collection, selection and customization of software, staff training, interfacing with current systems (where applicable), and gradual rollout of the system. An established CMMS company usually provides implementation support and resources so as to guarantee that there is a seamless transition.
The project takes approximately 4 to 8 Months (can be varied according to industry size and customer requirements)