According to:
- Preventive maintenance can yield an average of 545% ROI, as found in a study by Jones Lang LaSalle (Source: Sweeperland)
- 67% of manufacturers use preventive maintenance (Source: Worktrek)
- 80% of maintenance teams prefer preventive maintenance, while 51% use predictive maintenance (Source: Upkeep)
- 60% of businesses still rely on reactive maintenance (Source: Reliable Plant)
Preventive maintenance (PM) is a proactive approach to extending life, improving performance, and maintaining the reliability of mission-critical equipment. A preventive maintenance checklist is an essential component of this effort, offering precise, step-by-step instructions for regular maintenance. Standardizing maintenance procedures, and checklists assists teams in being better organized, more consistent, and more proactive at preventing unexpected downtime. This minimizes equipment downtime and the associated repair costs, enhances safety, and increases overall productivity.
To further automate maintenance activities, sophisticated tools such as Titan CMMS can be used. Such systems serve as a command center for maintenance personnel, providing checklists based on criteria and making workflow management easy. With effective CMMS implementation, organizations can achieve improved ROI, standardized operations, and better equipment reliability using a well-organized preventive maintenance checklist and advanced technology. Finally, preventive maintenance checklists are crucial for sustaining operational effectiveness and maximizing the value of critical assets.
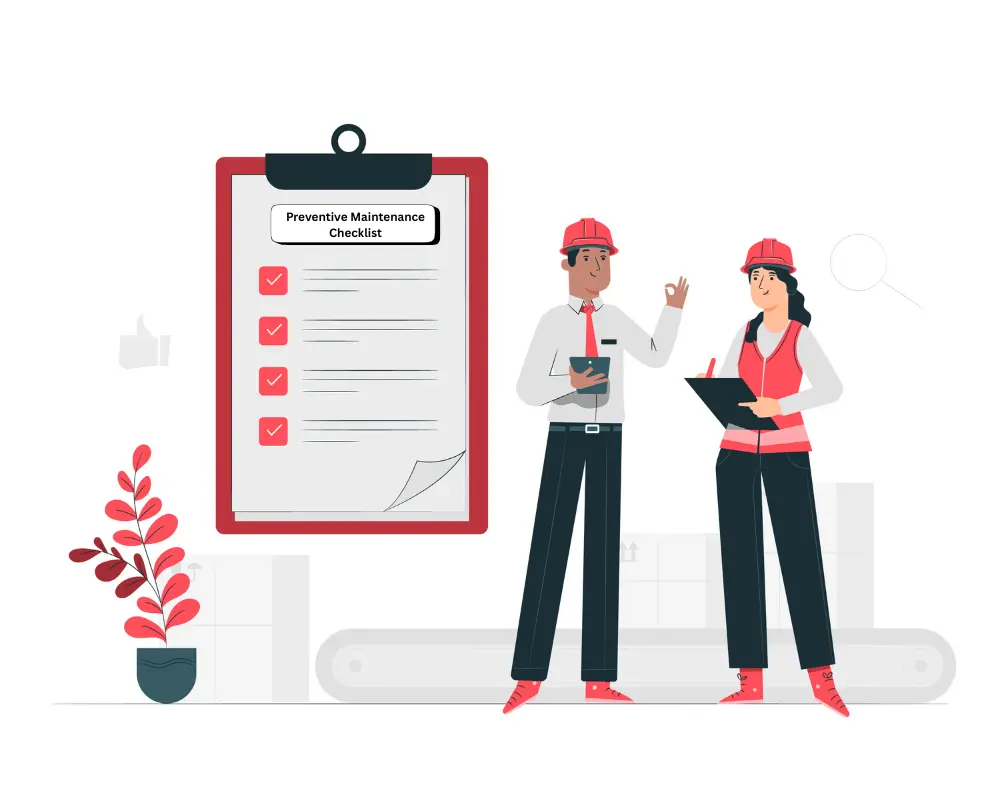
What is a Preventive Maintenance Checklist?
A preventive maintenance checklist is an organized document that defines routine maintenance procedures to maintain equipment in the best possible state. It may be a basic log or a comprehensive guide with safety guidelines and manufacturer specifications. Being the backbone of maintenance programs, it provides consistency and reliability. Developed by professionals, it ensures a reduction in failures, increases asset life and enhances efficiency. Following a checklist, maintenance teams avoid sudden breakdowns, lower costs, and improve safety. It finally guarantees proactive measures are taken, ensuring critical equipment remains in its best state of performance and ensuring operations are running smoothly. Proper execution avoids downtime and expensive repairs.
To Learn What is Preventive Maintenance? Click Here!
Importance of a Preventive Maintenance Checklist
- Reduces Unplanned Downtime: Regular maintenance helps prevent unexpected equipment failures.
- Extends Equipment Life: Proper care increases the longevity of machinery.
- Improves Safety: Identifying potential hazards early prevents workplace accidents.
- Saves Money: Preventing major breakdowns reduces costly emergency repairs.
- Enhances Productivity: Well-maintained equipment operates efficiently, improving overall output.
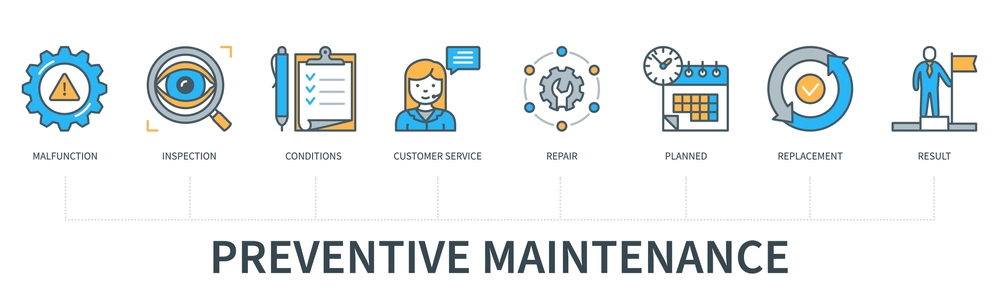
Types of Preventive Maintenance Checklists
1. Time-Based Preventive Maintenance Checklist
Scheduled at regular intervals (e.g., weekly, monthly, annually) regardless of equipment condition.
- Example: Monthly HVAC system filter replacement.
2. Usage-Based Preventive Maintenance Checklist
Performed after a specific usage level is reached (e.g., hours run, miles driven).
- Example: Vehicle oil change after 5,000 miles.
3. Condition-Based Preventive Maintenance Checklist
Tasks triggered by real-time monitoring and sensor data.
- Example: Replacing machine parts based on vibration analysis.
4. Predictive Preventive Maintenance Checklist
Utilizes AI and IoT to predict failures before they occur.
- Example: Predictive analytics for industrial equipment wear.
How to Create a Preventive Maintenance Checklist
Step 1: Identify Critical Assets
List all equipment that requires regular maintenance.
- Example: HVAC systems, production machines, vehicles, IT infrastructure.
Step 2: Define Maintenance Tasks
Specify tasks required for each asset.
- Example: Lubrication, filter replacement, software updates.
Step 3: Set Maintenance Frequency
Determine how often maintenance should occur.
- Example: Daily, weekly, quarterly, annually.
Step 4: Assign Responsibilities
Designate personnel responsible for each task.
- Example: Maintenance engineers, facility managers, IT administrators.
Step 5: Document and Standardize Procedures
Ensure consistency by documenting step-by-step procedures.
- Example: Standard operating procedures (SOPs) for machine inspections.
Step 6: Use Preventive Maintenance Software
Leverage CMMS (Computerized Maintenance Management System) for tracking and scheduling.
- Example: Automated reminders for upcoming maintenance tasks.
Step 7: Monitor and Improve the Checklist
Regularly review and refine the checklist based on performance data.
- Example: Adjust maintenance frequency based on historical failure rates.
Preventive Maintenance Checklists and Tasks
Here are some preventive maintenance checklists of machines, material handling equipment, facility infrastructure, network, and data systems. These can change based on the type of equipment, manufacturer instructions, and others.
Preventive Maintenance for Machines
- Inspect and clean filters.
- Inspect and tighten bolts and nuts.
- Inspect safety guards and other safety devices.
- Inspect and clean mechanical brakes or clutches.
- Inspect cooling systems, such as radiators or fans, for debris or damage.
- Check for leaks in hydraulic systems.
- Check lubrication levels and refill if needed.
- Check for proper alignment and adjust as necessary.
- Check for unusual vibration, noise, or other signs of wear.
- Clean and lubricate chains, gears, and sprockets.
- Verify proper operation of safety interlocks and limit switches.
- Test the machine’s operation to ensure it’s functioning properly.
Preventive Maintenance for Material Handling Equipment
Forklift Preventive Maintenance Checklist
- Inspect and clean air filters.
- Inspect brakes and replace worn or damaged parts.
- Check and adjust tire pressure.
- Check the battery and charging system.
- Verify the proper operation of the lift mechanism.
Conveyor Preventive Maintenance Checklist
- Check belt tension and alignment.
- Clean and lubricate chains or sprockets.
- Verify proper operation of motors and drives.
- Inspect safety guards and other safety devices.
Pallet Jack Preventive Maintenance Checklist
- Inspect brakes and replace worn or damaged parts.
- Check oil and hydraulic fluid levels.
- Verify the proper operation of the lift mechanism.
Preventive Maintenance for Facility Infrastructure
HVAC System Maintenance Checklist
- Clean or replace air filters.
- Inspect and clean ductwork.
- Test and inspect thermostats.
- Test safety switches and controls.
- Check and adjust refrigerant levels.
Plumbing System Maintenance Checklist
- Inspect and repair leaks in pipes and fixtures.
- Test emergency shutoff valves.
- Flush water heaters and tanks.
Electrical System Maintenance Checklist
- Inspect and replace worn wiring and cables.
- Test and calibrate electrical meters and instruments.
- Test and inspect UPS (Uninterruptible Power Supply) system.
Fire Protection System Maintenance Checklist
- Inspect and test fire pumps.
- Test and inspect fire extinguishers.
- Test and inspect fire sprinkler systems.
Security System Maintenance Checklist
- Inspect and test access control systems.
- Test and inspect surveillance cameras.
- Test and inspect alarms and intrusion detection systems.
Building Envelope Maintenance Checklist
- Inspect the roof for leaks or damage.
- Check the storm drains.
- Seal gaps or cracks in walls, windows, and doors.
Elevator and Escalator Maintenance Checklist
- Inspect and test elevator and escalator controls.
- Lubricate moving parts and adjust tension as necessary.
- Test and inspect emergency stop buttons.
Preventive Maintenance for Network and Data Systems
Server Room Maintenance Checklist
- Inspect and clean server room floors, walls, and ceilings.
- Test the backup generator and verify fuel levels.
- Check the server room temperature and humidity.
Network Equipment Maintenance Checklist
- Inspect and clean switches, routers, and other network equipment.
- Test and inspect wireless access points.
- Review and update network documentation.
Data Storage and Backup Checklist
- Inspect and clean backup tape drives or other backup devices.
- Review and update backup and disaster recovery plans.
Security and Access Control Checklist
- Test and verify access control systems.
- Inspect and test intrusion detection and prevention systems.
Determining the Frequency for Each Checklist
Setting the right frequency for each checklist is crucial for effective equipment maintenance:
- Daily Checklists: Quick inspections and safety checks, such as temperature monitoring or hazard identification.
- Weekly Checklists: Tasks that build on daily checks but do not require frequent completion.
- Monthly Checklists: More detailed inspections, such as replacing fluids or checking internal components.
- Quarterly Checklists: In-depth reviews, including third-party safety and compliance inspections.
- Seasonal Checklists: Adjustments for weather changes and operational shifts.
- Annual Checklists: Comprehensive evaluations, including disassembling machinery for thorough assessments.
With Titan CMMS, businesses can efficiently manage these schedules, ensuring proactive maintenance and reducing downtime.
To Learn How to Train Your Team for Effective CMMS Use Click Here!
Benefits of Preventive Maintenance Checklists
- Improved Equipment Performance – Avoids failures with routine inspections.
- Increased Equipment Lifespan – Detects issues early, enabling timely repairs.
- Improved Safety – Maintains workplace safety through equipment reliability.
- Cost Savings – Saves on emergency repairs and downtime costs.
- Regulatory Compliance – Assists in compliance with industry standards and regulations.
- Improved Efficiency – Maintains equipment at optimal performance.
- Improved Planning & Scheduling – Streamlines maintenance processes with automation.
- Better Documenting – Sustains updated maintenance records to support audits and troubleshooting.
- More Accountability – Ensures timely delivery of assigned maintenance tasks.
- More Communication – Streamlines team working through standardized maintenance processes.
- Lower Environmental Footprint – Reduces energy usage and waste through regular maintenance.
Why Choose Titan CMMS for Preventive Maintenance?
Titan CMMS is a cloud-based, mobile-enabled software platform that’s designed to improve preventive maintenance processes. It’s a centralized data repository for maintenance, which optimizes maintenance processes, automates reminders, and increases efficiency. With easy integration and professional customer service, Titan CMMS is the ideal choice for companies looking for proactive maintenance.
Conclusion
An efficiently designed preventive maintenance checklist is required to sustain operating effectiveness, lower downtime, and maintain safety. Organizations can establish a productive maintenance program by practicing the best techniques and utilizing digital resources such as Titan CMMS. Follow these steps today to enhance equipment reliability and overall productivity.