According to Plant Engineering and Fiix Software, Preventive Maintenance on a Hot Water Heater Includes inspections, flushing, and valve checks. It reduces downtime by 20-25%, extends lifespan by 15-20%, and cuts costs by 12-18%. Using a CMMS boosts efficiency by 25-30%, ensuring reliable hot water and energy savings.
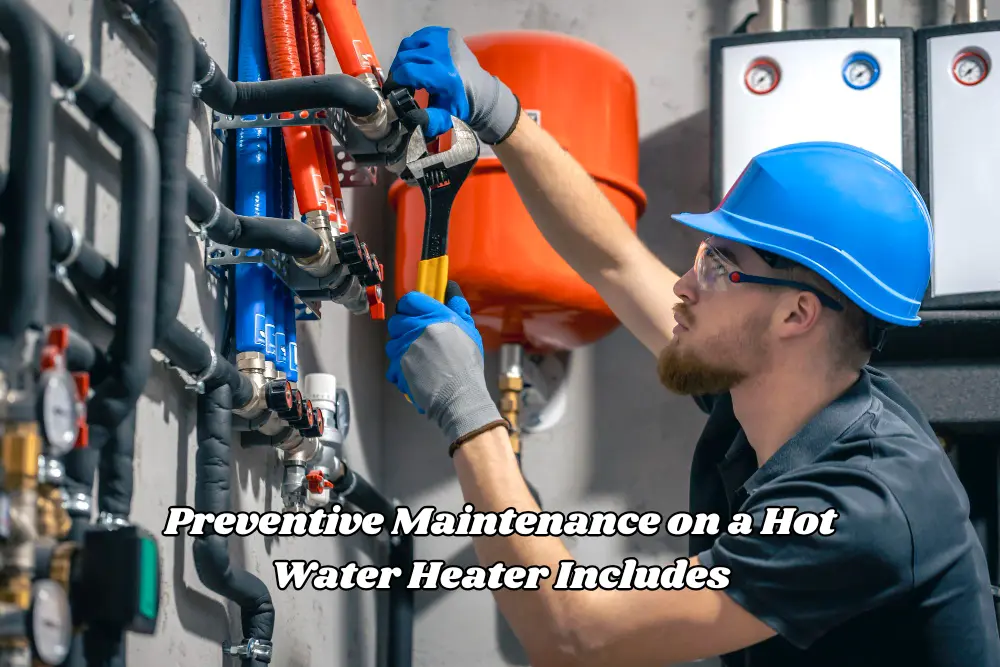
Introduction
A hot water heater is an essential appliance in any household, providing the comfort of warm water for various daily activities. However, like any other appliance, it requires regular maintenance to function efficiently and extend its lifespan. Preventive Maintenance on a Hot Water Heater Includes not only ensuring a consistent supply of hot water but also helping to reduce energy bills and prevent unexpected breakdowns. This comprehensive guide delves into the essential preventive maintenance tasks for hot water heaters, emphasizing the importance of each step and providing actionable insights.
Learn about Preventive Maintenance & CMMS Click Here!
What is hot water heater?
A hot water heater is designed to heat and supply hot water for domestic, commercial, or industrial use. It works by heating water using energy sources such as electricity, natural gas, propane, or solar power. There are two main types: storage tank water heaters, which store and continuously heat a volume of water, and tankless water heaters, which heat water on demand. Hot water heaters are essential for everyday activities like bathing, cleaning, and cooking, providing comfort and convenience by ensuring a steady hot water supply.
If you want to get a water Heater Click Here!
15 Steps for Effective Preventive Maintenance on a Hot Water Heater Includes
1. Understanding the Importance of Preventive Maintenance
Preventive maintenance involves regular inspections and jobs aimed at keeping the water heater in its optimal condition. Regular maintenance has several benefits:
- More Efficiency: A well-maintained water heater operates more efficiently, leading to less energy consumption and lower bills.
- Longer Lifespan: Regular maintenance can significantly prolong the life of the appliance, delaying the cost of buying an expensive new one.
- Safety Assurance: Regular inspections guarantee the detection of potential hazards, such as gas leakage or pressure build-up, and ensure the safety of the home.
2. Flushing the Tank to Remove Sediment Buildup
Over time, sediment and mineral deposits accumulate on the water heater tank bottom and affect its performance and efficiency. Annual flushing of the tank is essential to remove such deposits.
Steps to Flush the Tank:
- Switch Off the Heater: Switch off the power supply at the circuit breaker for electric water heaters and turn the thermostat to the “pilot” setting for gas water heaters.
- Shut Off the Water Supply: Shut off the cold water supply inlet valve in order to prevent additional water entry into the tank.
- Attach a Hose to the Drain Valve: Connect a garden hose to the drain valve on the bottom of the tank and direct the other end to an acceptable drainage point.
- Drain the Tank: Open the drain valve and allow the water to drain out, washing away sediment.
- Flush with Cold Water: Open the cold water supply for a brief period to stir up any lingering sediment, and then drain again.
- Close Valves and Refill: Shut off the drain valve, disconnect the hose, open the cold water supply, and restore the power or re-light the pilot.
3. Inspecting and Replacing the Anode Rod
The anode rod, or the “sacrificial” rod, attracts corrosive materials in water to avoid rust inside the tank. Maintenance and replacement are required to prevent corrosion of the tank.
Inspection Steps:
- Turn Off the Heater and Water Supply: For safety reasons, turn off the power and water supply.
- Locate the Anode Rod: Usually found on top of the tank, it may be covered by a plastic cap.
- Remove the Rod: Remove the rod using a socket wrench and inspect it.
- Inspect for Corrosion: If the rod is corroded or is of a smaller size, it has to be replaced.
- Install a New Rod: Apply Teflon tape on the threads and screw it in.
4. Testing the Temperature and Pressure Relief (TPR) Valve
The TPR valve is a safety mechanism for venting surplus pressure from the tank to prevent potential explosions. Proper operation is guaranteed by regular testing.
Testing Procedure:
- Place a Bucket: Place a bucket on the discharge pipe that is connected to the TPR valve.
- Raise the Valve Lever: Raise the lever slowly to allow water to drain out.
- Watch the Flow: A smooth flow means the function is correct; if water does not flow or still flows after dropping the lever, the valve should be replaced.
5. Adjusting the Thermostat for Optimal Temperature
Setting the water heater thermostat to the optimal temperature enhances efficiency and safety.
Recommended Settings:
- Temperature: Set the thermostat to 120°F (49°C) to balance comfort and energy efficiency.
- Safety: This setting reduces the risk of scalding and minimizes energy consumption.
6. Insulating the Tank and Pipes
Insulating the water heater tank and pipes reduces heat loss, improving efficiency and delivering hotter water faster.
Insulation Steps:
- Measure Tank and Pipes: Determine the measurements to purchase the correct insulation materials.
- Install Tank Insulation: Cover the tank with an insulation blanket, securing it with tape, being careful not to cover the burner or thermostat.
- Insulate Pipes: Insulate the initial few feet of the hot water and cold water pipes with foam pipe insulation.
7. Checking for Leaks and Corrosion
Regular inspections for leaks and corrosion help in the early detection of issues, preventing major problems.
Inspection Tips:
- Visual Check: Look for water pooling around the base and signs of rust on the tank and pipes.
- Address Issues Promptly: Tighten loose connections or consult a professional for significant leaks or corrosion.
8. Testing the Heating Element (Electric Heaters)
Electric water heaters rely on heating elements to warm the water. Testing these elements ensures they are functioning correctly.
Testing Steps:
- Turn Power Off: Ensure the heater is disconnected from the power source.
- Access Heating Element: Remove the access panel and insulation to expose the element.
- Test with a Multimeter: Set the multimeter to the ohms setting and insert the probes into the element terminals. The 10-30 ohms reading indicates an operating element.
- Replace if Needed: If the reading is below or above this range, replace the element.
9. Inspecting Gas Lines and Connections (Gas Heaters)
For gas water heaters, ensuring the integrity of gas lines and connections is crucial for safety and efficiency. A gas leak can be hazardous, so regular inspections are necessary.
Inspection Steps:
- Visual Inspection: Inspect the gas lines and connections for indications of wear, corrosion, or damage. Should you find any rust, cracking, or loose fittings, drastic action is imperative.
- Use a Soap Solution: Combine dish soap and water and use it on the gas connections with a sponge or spray bottle. If bubbles form, there is a gas leak.
- Listen for Hissing Noises: A low hissing noise around the gas lines might suggest there is a leak.
- Inspect the Pilot Light Flame: The pilot light must be a blue flame. A yellow flame or a flicker may reflect improper combustion or pressure problems.
- Get Professional Help: In case of a suspected gas leak, switch off the gas supply and contact a licensed technician.
10. Cleaning the Burner Assembly (Gas Heaters)
A dirty burner assembly can affect combustion efficiency, leading to higher energy consumption and potential carbon monoxide buildup. Regular cleaning ensures safe and efficient operation.
Cleaning Steps:
- Turn Off the Gas Supply: Shut off the gas valve to prevent leaks while working.
- Remove the Burner Assembly: Carefully detach the burner from the heater, following the manufacturer’s instructions.
- Clean with a Brush and Air Compressor: Use a wire brush to remove carbon deposits, followed by compressed air to clear any remaining debris.
- Check the Burner Ports: Ensure the burner holes are free from blockages.
- Reassemble and Test: Reattach the burner, turn on the gas, and check the flame pattern. A strong blue flame indicates proper combustion.
11. Checking the Venting System (Gas Heaters)
The venting system removes combustion gases from the water heater. A blocked or damaged vent can cause dangerous carbon monoxide buildup.
Inspection Tips:
- Check for Obstructions: Inspect the vent pipe for blockages caused by debris, bird nests, or corrosion.
- Look for Loose Connections: Ensure the venting system is properly secured to prevent gas leaks.
- Perform a Smoke Test: Light an incense stick near the draft hood while the heater is running. If the smoke is drawn into the vent, it is functioning correctly. If it lingers, the vent may be clogged.
- Carbon Monoxide Detector: Install a CO detector near the water heater for added safety.
12. Replacing Faulty or Worn-Out Parts
Over time, certain water heater components wear out and need replacement. Keeping an eye on these parts helps prevent unexpected breakdowns.
Common Parts That Require Replacement:
- Dip Tube: If you notice reduced hot water output, the dip tube may be deteriorating.
- Thermocouple (Gas Heaters): A faulty thermocouple may prevent the pilot light from staying lit.
- Heating Elements (Electric Heaters): If your water heater isn’t producing hot water efficiently, the heating elements might need replacement.
- Gaskets and Seals: Worn-out gaskets can cause water leaks.
13. Checking Water Pressure and Expansion Tank
Excessive water pressure can damage the heater and plumbing system. An expansion tank helps regulate pressure fluctuations.
How to Check Water Pressure:
- Use a Pressure Gauge: Attach it to a faucet and turn on the water. The ideal pressure should be between 40-60 psi.
- Install a Pressure Regulator: If the pressure exceeds 80 psi, a regulator can help prevent damage.
- Inspect the Expansion Tank: Tap the expansion tank—if it sounds full, it may need replacing.
14. Scheduling Annual Professional Inspections
While DIY maintenance is essential, scheduling a professional inspection at least once a year ensures deeper checks and repairs.
What Professionals Check:
- Internal Tank Condition: Using specialized tools, professionals can detect rust, corrosion, or leaks inside the tank.
- Gas Leak and Venting System: They verify proper combustion and ventilation.
- Electrical Connections (Electric Heaters): Ensuring safe and efficient power connections.
- Overall Efficiency: A professional may recommend upgrades or adjustments to improve performance.
15. Signs It’s Time to Replace Your Water Heater
Despite regular maintenance, all water heaters eventually need replacement.
Key Indicators:
- Age: If your unit is over 10-15 years old, consider upgrading to a more efficient model.
- Frequent Repairs: If you’re constantly fixing issues, a replacement may be more cost-effective.
- Discolored or Rusty Water: This could indicate internal tank corrosion.
- Strange Noises: Rumbling or popping sounds suggest excessive sediment buildup.
- Inconsistent Water Temperature: If your heater struggles to maintain the set temperature, it may be failing.
Conclusion
Regular Preventive Maintenance on a Hot Water Heater Includes flushing the tank, inspecting vital components, checking safety valves, and scheduling professional checkups. These steps ensure efficiency, longevity, and safety while preventing costly repairs. Whether you have a gas or electric water heater, following these maintenance tips will keep your system running at peak performance for years. Need help choosing a new energy-efficient water heater? Let us know!
Learn about Maintenance Management System Click Here!
FAQs
It’s recommended to flush your water heater once a year to remove sediment buildup and maintain efficiency.
Yes! Basic tasks like flushing, inspecting the anode rod, and testing the TPR valve can be done by homeowners. However, professional inspections are recommended annually.
Neglecting maintenance can lead to sediment buildup, inefficient heating, increased energy costs, leaks, and even premature failure of the unit.
If your water temperature fluctuates excessively or doesn’t heat properly, the thermostat may be malfunctioning and should be tested or replaced.
Yes! Insulating the tank and pipes can improve efficiency by 10-20%, reducing standby heat loss and lowering energy costs.