Introduction
Preventive maintenance is crucial for effective equipment management in various industries. It involves regularly inspecting, identifying, and fixing potential issues before they become major problems.
Think of preventive maintenance as a routine check-up for your equipment. As you go to the doctor for check-ups to stay healthy, your machines also require regular attention to perform at their best. This practice has become essential in:
- Manufacturing facilities
- Healthcare institutions
- Transportation systems
- Building management
- Industrial operations
The benefits of implementing preventive maintenance go beyond just taking care of your equipment. Organizations that embrace these practices often see:
- 50% reduction in equipment breakdowns
- 20-40% decrease in maintenance costs
- Extended equipment life by up to 75%
- Minimized unexpected downtime
- Enhanced workplace safety
Your dedication to preventive maintenance directly impacts the success of your operations. By proactively identifying and resolving potential problems, you establish a strong foundation for operational excellence. This approach helps you avoid expensive repairs, decrease unexpected equipment failures, and maintain consistent production schedules.
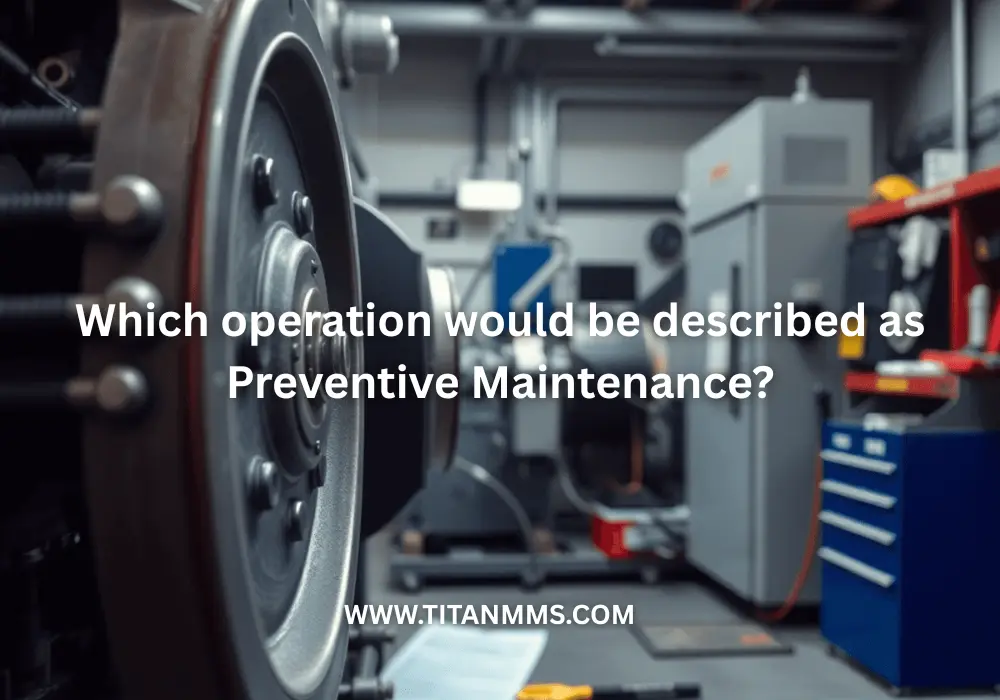
Understanding Preventive Maintenance Operations
Preventive maintenance represents a systematic approach to equipment care that focuses on preventing issues rather than fixing them after they occur. This proactive strategy involves regular, planned maintenance activities designed to keep machinery and systems running at peak performance.
Key Components of Preventive Maintenance:
- Scheduled Maintenance: Pre-determined intervals for maintenance tasks based on time, usage, or condition metrics
- Documentation: Detailed records of maintenance activities, equipment history, and performance data
- Resource Planning: Allocation of necessary tools, personnel, and materials for maintenance tasks
- Quality Standards: Specific criteria and benchmarks for maintenance procedures
The primary purpose of preventive maintenance lies in risk mitigation and asset preservation. By identifying and addressing potential issues early, you can avoid catastrophic failures that lead to costly repairs and production delays.
Benefits of Implementing Preventive Maintenance:
- Cost Reduction
- Lower emergency repair expenses
- Reduced replacement part costs
- Minimized energy consumption
- Optimized inventory management
- Performance Enhancement
- Increased equipment reliability
- Enhanced production quality
- Improved safety conditions
- Reduced unexpected breakdowns
- Asset Management
- Extended equipment lifespan
- Better resource utilization
- Improved resale value
- Enhanced warranty compliance
Different industries implement varying types of preventive maintenance strategies based on their specific needs:
- Time-Based Maintenance: Fixed schedules regardless of equipment usage
- Usage-Based Maintenance: Activities triggered by operational metrics
- Condition-Based Maintenance: Tasks determined by equipment performance indicators
The success of preventive maintenance depends on consistent execution and proper documentation. Companies that maintain detailed records of their maintenance activities can better predict equipment behavior and optimize their maintenance schedules.
Common Operations Described as Preventive Maintenance
Preventive maintenance includes several important tasks that help keep equipment working properly and avoid unexpected breakdowns. Let’s take a look at these essential maintenance practices, starting with regular cleaning procedures.
1. Regular Cleaning
Clean equipment works better, lasts longer, and needs fewer repairs. Dust, dirt, and other substances can greatly affect how machines operate and cause them to wear out earlier than expected. Here’s what you should know about cleaning your equipment:
Key Areas That Need Regular Cleaning:
- Air intake systems and filters
- Moving parts and mechanical components
- Electrical connections and control panels
- Cooling systems and heat exchangers
- Production line equipment
Cleaning Requirements for Specific Equipment:
- Manufacturing Equipment: Wipe down surfaces daily, deep clean components weekly
- HVAC Systems: Change filters quarterly, clean ducts annually
- Office Equipment: Clean printers, scanners, and computers weekly
- Industrial Machinery: Schedule cleaning based on how often it’s used and the conditions it’s exposed to
Best Practices for Keeping Workspaces Clean:
- Create a cleaning schedule with clearly defined responsibilities
- Use the right cleaning materials and solutions for different types of equipment
- Write down cleaning procedures to ensure consistency
- Train staff on proper cleaning techniques
- Keep records of cleaning activities for tracking and compliance purposes
Benefits of Regular Cleaning:
- Fewer instances of equipment failure
- Longer lifespan for components
- Better quality products
- Safer workplace environment
- Lower maintenance costs
Standards for Professional Cleaning:
- Follow manufacturer guidelines when it comes to cleaning procedures
- Use cleaning agents that are approved by the industry
- Wear appropriate protective gear during the cleaning process
- Clean equipment during scheduled downtime periods
- Check cleanliness using inspection checklists
Regular cleaning is a fundamental part of effective preventive maintenance. By maintaining a clean working environment, you not only ensure that your equipment operates at its best but also make it easier to identify potential problems during routine inspections.
2. Lubrication
Proper lubrication is a crucial part of preventive maintenance, acting as a lifeline for machinery components. The main purpose of lubricants is to create a protective barrier between moving parts, reducing friction and preventing metal-to-metal contact that leads to wear and tear.
Common Types of Lubricants:
- Oil-Based Lubricants: Ideal for high-speed applications, used in engines, gearboxes, and hydraulic systems, providing excellent heat dissipation.
- Grease: Perfect for slow-moving components, stays in place longer than oil, suitable for bearings and joints.
- Synthetic Lubricants: Enhanced performance in extreme temperatures, extended service life, used in specialized industrial equipment.
The selection of appropriate lubricants depends on several factors:
- Operating temperature range
- Speed of moving parts
- Load conditions
- Environmental factors
- Equipment manufacturer specifications
Regular lubrication schedules should align with equipment usage patterns and operating conditions. Mastering lubrication programs with best practices can lead to optimal machinery performance. Under-lubrication can lead to increased friction and premature wear, while over-lubrication might cause seal damage and waste resources. Maintaining detailed lubrication logs helps track service intervals and identify potential issues before they escalate into major problems.
3. Routine Inspections
Regular inspections are your first line of defense against equipment failures. These systematic checks help identify potential issues before they escalate into major problems that could halt operations.
Visual Assessments
- Check for visible wear patterns
- Identify loose components or connections
- Spot leaks, cracks, or unusual discoloration
- Monitor belt tension and alignment
- Detect corrosion or rust formation
Functional Testing
- Measure equipment vibration levels
- Test operating temperatures
- Record power consumption patterns
- Verify speed and performance metrics
- Check noise levels during the operation
Inspection Scheduling
- Daily walk-through checks
- Weekly component-specific inspections
- Monthly comprehensive assessments
- Quarterly specialized testing
- Annual full-system evaluation
The effectiveness of routine inspections relies heavily on proper documentation. Creating detailed inspection checklists helps maintain consistency and ensures no critical components are overlooked. These records also establish valuable baseline data for tracking equipment performance over time.
Modern inspection methods incorporate digital tools and sensors for enhanced accuracy. Thermal imaging cameras detect heat variations, ultrasonic devices identify internal wear and vibration analyzers measure mechanical imbalances. These technologies complement traditional visual inspections by revealing issues invisible to the naked eye.
4. Replacing Worn Parts Proactively
Proactive component replacement is a crucial part of effective preventive maintenance. You can identify parts that are nearing the end of their service life by using the following methods:
- Manufacturer specifications and recommended replacement intervals
- Historical performance data
- Visual wear indicators
- Vibration analysis results
- Temperature monitoring readings
The cost of scheduled part replacements is significantly lower than emergency repairs. For example, a failed bearing might cost $1,000 to replace during an unplanned shutdown, while the same replacement during scheduled maintenance costs only $200-300.
Key benefits of proactive replacements:
- Minimized production downtime
- Reduced risk of catastrophic equipment failure
- Lower repair costs
- Extended equipment lifespan
- Improved workplace safety
To achieve optimal results, make sure to keep detailed records of component lifespans and create a systematic replacement schedule based on usage patterns and manufacturer guidelines.
Conclusion:
Preventive Maintenance involves routine tasks like inspection, cleaning, and part replacement to prevent equipment breakdowns and optimize performance. It minimizes downtime, repairs, and expenditure, while enhancing operational efficiency. Using a CMMS (Computerized Maintenance Management System) makes it easy to schedule, document, and track maintenance work. Preventive Maintenance plays an important role in sustaining asset reliability, safety, and lifespan, and thus the key to effective maintenance management across any industry.
FAQs (Frequently Asked Questions)
Q1. What is preventive maintenance?
Ans. Preventive maintenance refers to proactive measures taken to maintain equipment and machinery in optimal condition. It involves regular inspections, cleaning, lubrication, and replacements to prevent potential failures before they occur.
Q2. Why is preventive maintenance important in various industries?
Ans. Implementing preventive maintenance operations is crucial as it leads to improved efficiency, reduced operational costs, minimized downtime, and enhanced lifespan of equipment across various industries.
Q3. What are some common operations involved in preventive maintenance?
Ans. Common operations that fall under preventive maintenance include regular cleaning of equipment, lubrication techniques to reduce friction, routine inspections for wear and tear identification, and proactively replacing worn parts.
Q4. How does regular cleaning contribute to preventive maintenance?
Ans. Regular cleaning is essential in preventing malfunctions and ensuring optimal performance of machinery. It helps avoid dirt buildup that can lead to operational issues and maintains workspace hygiene.
Q5. What role does lubrication play in preventive maintenance?
Ans. Lubrication minimizes friction between moving parts, reducing wear and tear on machinery components. Different types of lubricants are used across industries based on their specific applications to ensure efficient operation.
Q6. Why are routine inspections necessary in preventive maintenance?
Ans. Routine inspections are vital for detecting early signs of deterioration or malfunction in critical equipment. They involve visual assessments and functional tests that help identify potential issues before they escalate into costly breakdowns.